Roofing Design Considerations
Condensation Control and Ventilation As Building Regulations demand ever-higher thermal efficiency, today’s buildings are becoming increasingly airtight. While this is undoubtedly beneficial for building energy performance, architects and contractors must understand the implications for moisture and vapour management when considering roofing membranes.
Condensation control should be considered as part of the design process. Successful control will depend on factors such as prevailing winds, room layout, number of storeys and type of heating system as well as the more usually accepted aspects such as construction, heating, ventilation and moisture production. All these aspects, therefore, should be considered carefully and, as they are interdependent to a greater or lesser degree, they should be considered together.
The fundamental principle in designing to minimize condensation is to maintain a balance of the three factors 1. Thermal and vapour properties of the structure 2. Heat input and 3. Ventilation to achieve either low vapour pressure and/or high structural temperature.
The building fabric, typical weather conditions and anticipated occupancy patterns and uses will all interact to define the moisture risks associated with the construction. These “ground rules“ form the basis of a good hygrothermal design strategy. Once an understanding of the building, weather and occupancy are achieved, the designer can then focus on ensuring the heat, air and moisture movement within the structure is properly balanced. This ensures both a healthy environment for the occupants of the building and long life for the building.
Brent Jones - A L King Roofing Ltd
“Proctor Air has been very popular since we started stocking it at the beginning of the year, we have seen the demand for a robust and reliable Air permeable membrane more than ever in recent months and Proctor Air totally fits the bill!”
Articles
How Roof Underlay Specification Can Help Make a Retrofit Project a Success
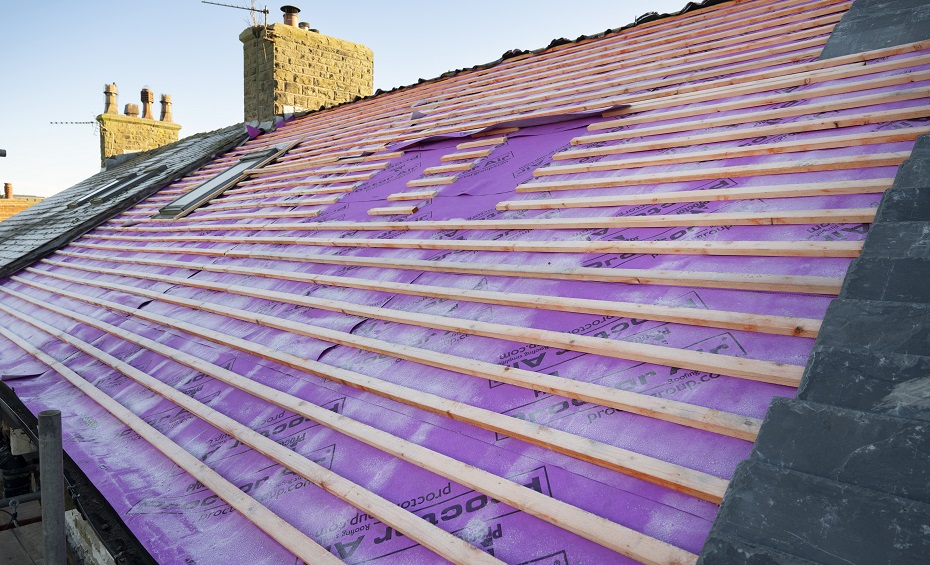
All roof coverings and underlays need to be replaced at some point during a building’s useful life. When that time comes, how can the next generation of roof membranes help existing buildings to meet current performance requirements and be resilient
for the future? Pamela Howat, Senior Technical Advisor at A. Proctor Group looks at some of the challenges of retrofitting roofs.
Perhaps the biggest challenge presented by existing buildings is that no two projects are ever the same. The construction method and the quality of the construction, combined with site specific factors that affect exposure to weather, all influence the durability of a roof. Any resulting water ingress will have a further negative impact on lifespan…
How to Install Wraptite®
Uncontrolled air leakage through cracks, gaps and improperly sealed elements in a building façade contribute to a significant reduction in the energy efficiency of the entire construction. In some case, such air leakage can reduce the effectiveness of an insulated envelope by up to 70%. Ensuring airtightness is crucial in mitigating heat loss and minimising building emissions. The A Proctor Group provide the Wraptite membrane to facilitate better airtightness across the façade. This is our fully self-adhered, airtight and vapour permeable membrane, which is fully BBA certified for use in walls, roofs and floors. It is also a Passive House certified airtightness component, and has been used to achieve very low levels of air permeability.
Wraptite has potential uses across a number of applications, from spanning sheathing boards on framed buildings; to diminishing draughts in masonry walls. It is typically applied across the sheathing board on timber or steel framed roofs and walls, or over other monolithic elements such as a CLT structure…
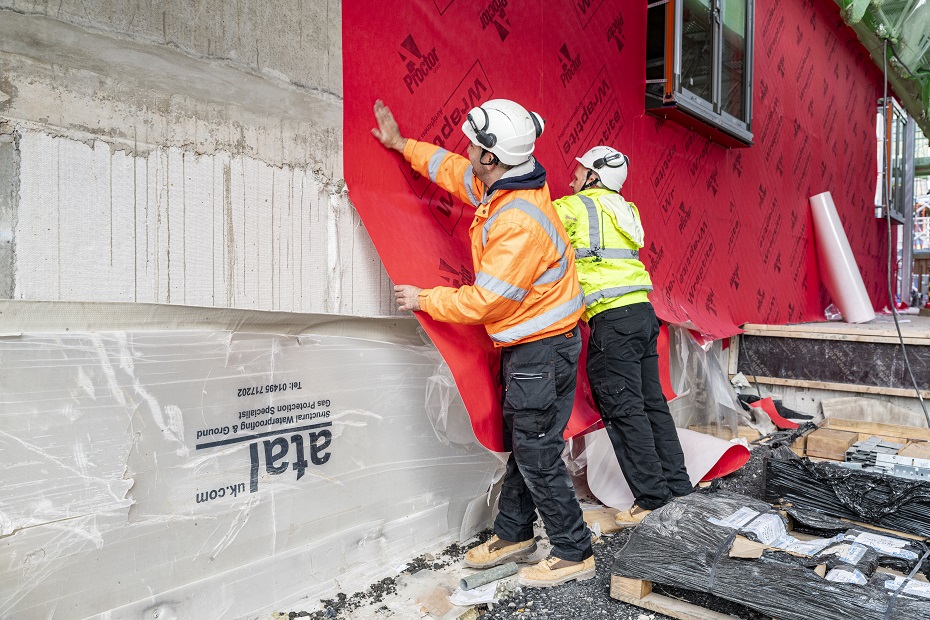
Is the Future Warm Roofs?
The A Proctor Group have been supplying construction membranes for over 30 years, and then, as now, most of the mainstream housing in the UK was built using truss rafters with insulation placed across the ceiling. This type of construction, a “cold pitched roof”, leaves a large, unheated, and uninsulated void above the habitable spaces.
Prior to the common usage of trusses, which began in the 1960s, these roof spaces were made from a frame of cut timbers, which allowed a relatively easy path to convert the loft space in the future, as is the case in many older properties. Trusses make this process all but impossible, but at the time this space was still a useful storage area, often floored, but not really useful as living space…
Proctor Air®: Revolutionising Pitched Roofing Amidst Climate Change Challenges
Recent weather in the UK has shown the effects of Climate Change. The UK climate change projections programme (UKCP) shows that over the next half century, the UK is expected to experience:
• Warmer and wetter winters, and hotter drier summers.
• A higher frequency and intensity of extreme weather events, including torrential rain and heatwaves.
• Clearer skies in summer
With this in mind, the construction industry must adapt. This includes roofing which may need to relook at roofing traditional practices. Will metal sheets replace discontinuous covering such as slates and tiles? Is there a further argument for off site roofing practices and can the underlay be used as a temporary cover, even in extreme weather?
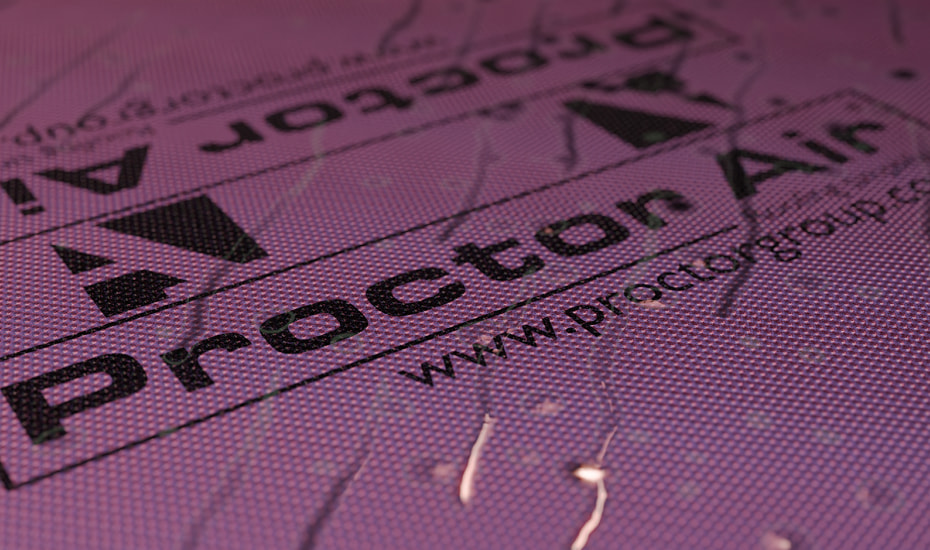