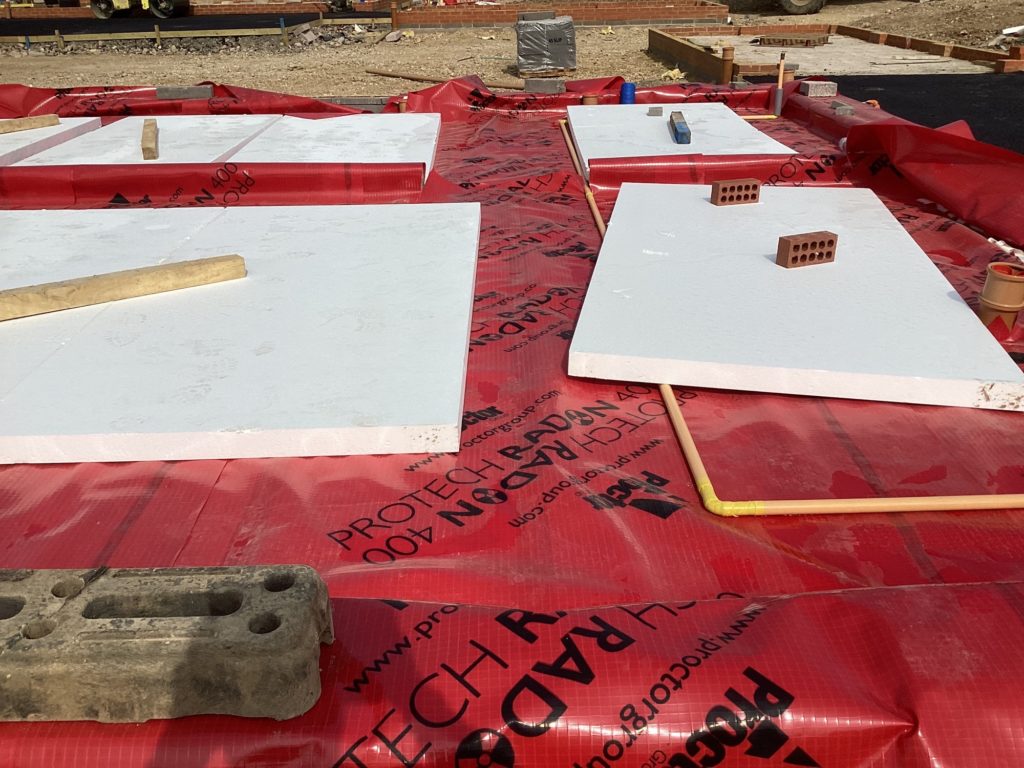
Radon in Buildings
The average UK household radon level is 20 Bq/m³. The current ‘action level’ for residential buildings is 200Bq/m³. If the radon level is at or above the action level, protective measures must be taken to reduce the ingress of the radon.
There are several main routes of ingress for radon or any other ground gas. These include cracked or porous solid floors, junctions and joints between components, cracked or porous below-ground walls such as in basements, gaps in suspended floors, porous walls and foundations, gaps at service penetrations and pipes and through cavity walls.
Due to the geological origins of radon gas, there is generally no scope to remove or neutralise the source of the gas, so barrier and venting solutions are most commonly employed. However, limiting the extent of the ingress paths here can help by reducing the long-term reliance on a barrier and providing additional protection.
Low-risk areas with less than a 1% chance of exceeding action levels do not require any special measures to be taken. Sites between 3 and 10% are classed as medium risk and require a basic level of protection, with sites over 10% being high risk and requiring full protective measures. Basic protection comprises a radon barrier membrane within the floor or solum of the building, linked to a damp proof course in the wall.
This barrier system should extend across the entire footprint of the building, including the cavity, and all overlaps and service penetrations should be fully sealed. Full protection requires a radon barrier membrane but supplements this with additional ventilation to increase the rate of gas exfiltration. The ventilation can be a ventilated void. If there is no void, then a radon sump should be installed. Ventilation systems are usually passive, with the option to convert to active by adding mechanical extraction fans. Active ventilation is only necessary if radon levels are above the action level, even with a barrier membrane and passive ventilation.
Selecting and Installing
Ensuring a barrier membrane system works effectively requires the material used to be suitably robust and the system to be well installed. Like other ground gas protection measures, the system is only as good as its installation, and if joints are not properly sealed or the membrane is punctured, then adequate performance cannot be guaranteed. However, a properly designed and fitted barrier will also function as a damp-proofing membrane.
The BBA requires radon barrier membranes to be at least 0.4mm, or 400 microns in thickness. It’s important to remember, though, that membranes, if stretched, will become thinner, so ensuring that the material has good tensile strength and elongation characteristics will ensure that the membrane retains its properties.
When installed under a slab, for example, concrete poured on top can exert forces on the material, causing it to stretch, and become thinner, creating a zone where the permeation of gas becomes more likely, even if the membrane is still intact and unbroken. This is the risk of using unreinforced DPM-style membranes for radon protection. Membranes made from 100% virgin polymer with a polyester reinforcing scrim have the optimal mechanical strength properties thickness for thickness and provide excellent robustness and minimal elongation under load.
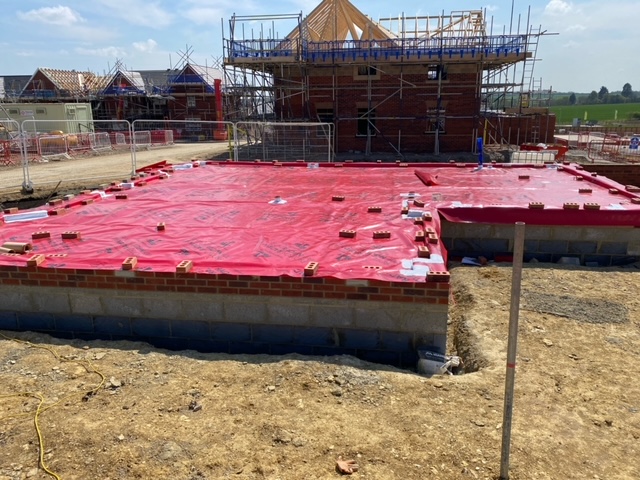
Once the membrane is installed, it should be thoroughly inspected prior to covering, as fixing any issues after the membrane is covered is often effectively impossible. This inspection should look for continuity issues such as unsealed joints, unsealed penetrations such as waste pipes, and punctures. Finally, although it may seem obvious, it’s also essential that the protective membrane and any associated accessories, such as DPCs, extend across the entire footprint of the building, from external to external, closing off any potential gas ingress points. This includes closing off any cavity walls with a suitably sealed and gas-resistant DPC.
Protection of Basements
It’s crucial that any basements or occupied underground spaces are protected, particularly as radon can permeate not only through the floor but also through the retaining walls. For a typical domestic house, the areas in contact with the ground could be several times higher than for a similar house without a basement. This risk is further compounded by the lack of natural ventilation in spaces below ground level.
Alongside this, it’s also important to consider waterproofing when creating a new basement or converting an existing cellar. Guidance and recommendations for basement waterproofing are given in BS 8102, which also advises on the importance of considering radon mitigation when designing basements. In these situations, it’s usually advisable to appoint a specialist to design and install the combined system, as radon and waterproofing requirements can sometimes conflict.
Radon Protection for Extensions
While providing protection to an extension when there’s none in the existing building may seem pointless, a subfloor depressurisation system can help provide some degree of protection to the existing structure. Space for a sump under the existing structure can be created by locating the new sump and extraction pipework adjacent to the existing structure and knocking through the existing wall. The new depressurisation system can therefore extract from the fully protected extension and the existing unprotected structure via the two linked sumps.
Want to know more?
Further guidance on radon from the UK Health Security Agency
Further information on the A Proctor Group’s radon protection systems
*article published in Housebuilder and Developer Jan 24
Request a Sample
Book a CPD
Technical Advice
U-Value Calculation
Specification Check
CAD Detail Review