Increasingly, there is recognition of the urgent need to improve the energy efficiency of buildings. In doing so, national, and global strategies for retrofitting existing buildings are crucial. In addition, the efficient use of resources, minimising waste, and preserving and extending the lifecycle of buildings is equally important. The incredible value of preserving our heritage is fundamental to the core of our society, preventing the waste of resources and energy, and can genuinely be said to be securing the future for generations to come.
For all work to a listed building that involves alterations, extensions or demolition and will affect its character externally and in some cases internally, Listed Building Consent is required. The restrictions that apply to alterations to listed buildings can be significant and challenging, particularly concerning energy efficiency and condensation control. However, there are solutions at hand. Some of these are identified below.
Strategies to upgrade the energy performance of existing buildings must be considered carefully and holistically, as actions affecting one aspect of the building may have unforeseen consequences in another. For example, in our approach to building refurbishment, we must recognise that we cannot simply upgrade thermal insulation without addressing the balance of moisture movement and air leakage.
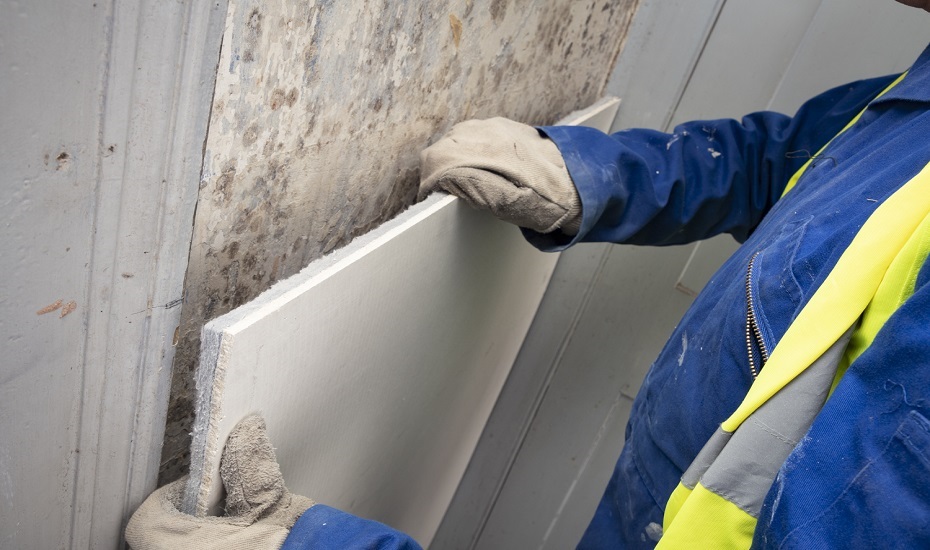
Thermal Insulation – air leakage and airtightness
When considering the insulation of buildings, we usually refer to U-values. A U-value quantifies the rate of heat loss through a building element such as walls, roof, windows, and doors. The lower the U-value is, the slower the heat generated by the heating system will escape the building, and the less energy input is required to maintain a comfortable internal temperature.
While not factored into U-value calculations, air leakage through cracks, gaps, holes, and improperly sealed elements such as doors and windows can cause a significant reduction in the performance of even thermally insulated envelopes. The industry is increasingly turning to air barrier membranes as an essential part of the process in achieving the most effective means of controlling and reducing air leaks.
Modern new build homes typically have wall U-values of around 0.2 W/m2 with solid walls will be more like 2.0 W/m2 magnitude worse, which will have a significant effect on the heating bills of the property and the quality of life of the occupants. This has substantial impacts where occupants are in fuel poverty or belong to a vulnerable social group such as the elderly. For such groups, poor thermal insulation can lead to health problems, so it’s essential that upgrading such homes is a priority
In listed buildings, this priority will need to be balanced against retaining architectural features, maintaining the character of the building and aesthetic qualities, and ensuring the internal spaces remain large enough to be fit for purpose.
Interior Wall Insulation in the refurbishment of listed buildings
There are some challenges when considering the right choice for refurbishment projects of listed buildings. Constructions of solid masonry, as tends to be the case for most older buildings. The traditional building materials used in these older properties, such as lime-based mortar and plaster, have very different hygrothermal properties from their modern equivalents. Adding insulation of low permeability, such as rigid foam, can result in damaging moisture problems for two primary reasons.
Adding any internal insulation will reduce the temperature of the existing wall masonry, making it more likely that condensation will occur to the inside as there will be less heat penetrating from the living spaces to warm up the masonry. Secondly, some insulation types, such as rigid foams, can prevent the drying out inwards into the building, further compounding the problem. If not adequately accounted for in the design, this moisture accumulation can continue unchecked, increasing issues with dampness and mould over time and, in extreme cases causing the masonry to degrade due to freeze/thaw cycling.
Permeable insulation prevents moisture from being trapped in the construction and minimises disruption of the established balance of moisture flows within the building fabric to the same degree. However, traditional moisture vapour permeable insulation, such as mineral fibre, tends to be very bulky. This results in another challenge in historical refurbishment: preserving interior space.
Solid wall construction – external or internal insulation
Protected historic listed buildings are often solid wall construction, and a commonly held perception is that it isn’t possible to insulate externally and not practical to insulate internally. Preserving the external features of the property excludes the traditional approach to solid wall insulation. A traditional external application would be achieved through insulated boards being secured to the external face with a render finish. The drawback of this method is the change in the overall appearance of the dwelling.
Internal approaches typically include the application of insulated plasterboard fitted to the walls of each room and then a subsequent plaster finish. The materials suitable for internal insulation can result in an overall reduction of floor space, and therefore the use of these traditional methods can often be impractical due to space constraints.
The A. Proctor Group developed Spacetherm® WL, a laminate specifically intended for use where improved thermal performance is required with limited space. Spacetherm WL is fixed to the internal surfaces of existing solid walls without the need for mechanical fixings. Consisting of a Spacetherm aerogel insulation blanket bonded to 3mm Magnesium Board (MgO), at just 13mm thick, there is often no need to remove skirting boards and cornices, saving time and cost. Typically, a solid wall will have a U value of around 2.1 W/m2 K. Following the application of Spacetherm WL this can be reduced to around 0.8 W/m2K, dependent on the wall materiality and thickness.
Spacetherm WL is supplied in a 1200 x 600 mm panel weighing just 4.9 kilograms, meaning that sheets are easy to handle by one person. Once installed, the system provides a significant reduction in heat loss. In addition, a nominal 13 mm increase in wall thickness means that sockets, switches, and TV/network points can be left in situ and features such as cornices and windowsills can be left as is, with little or no modification required.
An internal insulation system using materials such as mineral fibre, wood fibre or natural wool has a relatively high thermal conductivity, and therefore requires a significant depth of insulation to achieve modern thermal standards. Due to the depth required, these materials are typically installed within a freestanding frame, with a cavity to isolate them from the masonry. This can result in a system depth of over 200mm, which is impractical to incorporate into an existing space. In comparison, a system installing Spacetherm insulation directly to the masonry could achieve similar thermal values in only 50mm of depth. This makes Spacetherm ideal for use in rooms with limited floor area, at door and window reveals, and in other areas where retaining existing features would otherwise limit the use of thick and bulky insulation.
The thermal conductivity of Spacetherm at 0.015 W/mK makes it among the best thermal insulants in use today, which, combined with its high vapour permeability, makes it ideal for refurbishments. Furthermore, Spacetherm aerogel is also hydrophobic, meaning it actively repels liquid water. Spacetherm can be used directly in the blanket form under render or plaster, utilising its inherent flexibility to fit around curved or uneven wall surfaces, or it can be laminated to a variety of panels and lining boards for more specific applications. Because the aerogel insulation blanket contains no blowing agents, it does not release harmful gasses into the building over time, nor does its performance degrade, with extensive testing showing no loss of thermal performance over 50 years.
Thermal upgrades to older listed properties may be avoided due to the cost and problems associated. Therefore, thin systems such as Spacetherm-WL offer a simple option where a traditional thermal upgrade is impossible.
Although this system typically won’t achieve a thermal performance in line with building regulations, even a small upgrade in thermal insulation can raise the internal surface temperature enough to avoid condensation problems. The minimal thickness also allows it to be used in space constrained areas to ensure continuity of thermal insulation.
For example, a solid masonry wall could be prone to surface condensation, particularly around window interfaces. This is especially true if the wall is insulated, but the window reveals are not. If insulation is added to the main wall surface but omitted from the reveals, although the wall surface temperature increases, the surface temperature in the windows reveals decreases, leading to increased condensation risk in these areas. Even adding a minimal amount of insulation to the reveals will elevate this temperature enough to mitigate this condensation risk, highlighting the importance of a continuous envelope of thermal insulation.
Exterior Facade Solutions – air leakage and thermal bridging
At the more extensive end of refurbishments are façade retention projects, where most of the building is demolished and replaced with a modern new-build structure, retaining only the facade from the existing structure.
While this method resolves some of the inherent issues in such projects, simply replacing the problematic elements and features with modern equivalents, designing an effective interface between what is replaced and what is retained can still be challenging.
Air leakage and cold bridging are the most significant problems to be overcome in these areas, so by combining a vapour-permeable, self-adhering, air barrier membrane with a layer of high-performance insulation, Wraptherm® offers a compelling and straightforward solution to these issues.
Wraptherm is installed on the reverse of the retained facade stonework. However, as Wraptherm is vapour permeable, it does not adversely affect moisture movement through the facade stonework. This helps limit damage that can occur when moisture flow through older stonework is altered by refurbishment works.
Inside of solid Masonry, Wraptite’s water resistance shouldn’t be a factor. I would remove the line about water ingress. By sealing tightly to door and window frames and other penetrations, also limits heat loss associated with air leakage. The unique layer of aerogel insulation in the Wraptherm also effectively limits cold bridging by providing a continuous insulation layer across the back of the facade. Hence, there is a thermal break between the new structure internally and the cold outer stonework, further boosting the energy performance of the upgraded building. Combining these properties into a single material, Wraptherm speeds up and simplifies the installation process and reduces on-site defects and requirements for costly remediation.
Solutions are at hand in meeting the need to address the energy efficiency of buildings, maximise resources, and mitigate waste. The A. Proctor Group recognises the restrictions that apply to the alterations possible with listed buildings and continues to lead the way on innovative, technologically advanced solutions that address the fundamental demands of energy efficiency, airtightness, and condensation control.
Article by Callum Anderson Technical Advisor published in ADF March 2023
Request a Sample
Book a CPD
Technical Advice
U-Value Calculation
Specification Check
CAD Detail Review