The higher performance targets within the new building regulations specify that CO2 emissions for dwellings are to be reduced by 31% and for all other buildings by 27%. These new requirements are a move towards the Future Homes Standard and Future Buildings Standard awaited in 2025. With a target for all new homes in England built from 2025 to achieve a 75% reduction in carbon emissions, the latest changes to part L are only part of the story. This latest interim uplift in standards is a push towards fabric-first principles such as:
- Considering the design and construction of the building envelope in the initial design stages
- Robust detailing
- Understanding the principles of airtightness requirements and ventilation
- Reducing thermal bridges
- Utilising materials that can prove compliance with regulatory requirements
- Maximising solar gain through building orientation with respect to overshadowing
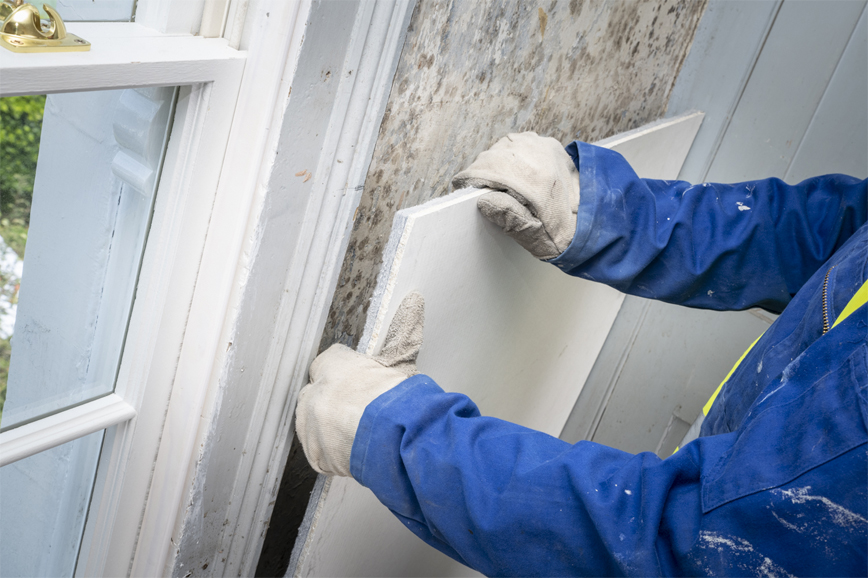
Limiting Standards for New Dwellings
The updated limiting U-values for insulating new fabric elements and air permeability in new dwellings are outlined in terms of the Maximum U-value W/m²K.
The new Part L gives air permeability (air leakage rate) limiting values in new dwellings as 8.0m3/(h.m2)@50 Pa, compared to 10.0m3/(h.m2)@50 Pa previously. However, it is still high compared to some European countries, with many already below 5.0m3/(h.m2)@50 Pa. Airtightness is the resistance of the building envelope to infiltration when ventilators are closed. A more robust airtightness target would have resulted in airtightness being more seriously considered by building designers as a measure for energy efficiency to complement thermal measures.
Part L acknowledges the importance of getting airtightness right, explicitly mentioning that “when carrying out work in new dwellings, care should be taken to reduce unwanted heat loss through infiltration.” For example, highlighting the challenges of potential penetration of the air barrier as a result of internal building services and structural penetrations. The use of an external airtight barrier such as Wraptite® from the A. Proctor Group is specifically designed to overcome the risk of damage to the traditional internal air barrier approach that can occur with internal service works.
Concerning Thermal Bridging in new dwellings, Part L notes that at the product specification stage, “opportunities should be considered to use products that help to reduce thermal bridges.” In addition, “the products used should be those shown in the original design. If a product is substituted, the revised specification should be reflected in the SAP calculation and report in the Building Regulations England Part L compliance report (BREL report).”
The heat loss caused as a direct result of thermal bridging will lead to increased energy costs for buildings and homes. It is estimated that thermal bridges can account for 20-30% of the heat loss in new build houses.
Meeting Part L – Solutions for Airtightness
Without adequate air barrier protection, the problem of air leakage through cracks, gaps, holes, and improperly sealed elements such as doors and windows causes a significant reduction in the performance of even thermally insulated building envelopes. With the increasing requirements and emphasis on thermal insulation, the proportion of energy lost through air leakage has become more crucial. However, thermal insulation will be rendered ineffective unless the airtightness of the structure is addressed. Air leakage dramatically reduces the effect of thermal insulation and must therefore be a critical focus.
The two main ways to achieve airtightness in the building envelope are internally or externally (“inside or outside the services zone’.) The use of traditional internal air barriers can be more complex and costly to install due to the need to accommodate building services such as electrical, lighting, heating, and drainage systems. Part L acknowledges the challenges of potential penetration of the air barrier as a result of internal building services and structural penetrations. The internal air barrier is only as good as the quality of its installation.
By moving the air barrier to the external side of the structural frame, external air barrier systems such as Wraptite from the A. Proctor Group allow for an almost penetration-free airtight layer that can be installed faster and more robustly. Far simpler than internal options, an external air barrier system like Wraptite will maintain the envelope’s integrity, with fewer building services and structural penetrations to be sealed and less room for error.
The traditional forms of VCLs and airtightness membranes will often require mechanical fixing. The self-adhered nature of Wraptite allows for a fast and straightforward installation process, minimising the use of additional sealants and tapes and requiring no specialist contractors to achieve a robust result. This one-step solution provides an air barrier layer and effective secondary weather protection in one installation process, allowing a wind and watertight envelope to be achieved more quickly than traditional methods
Meeting Part L – Solutions for thermal bridging
A popular measure of tackling thermal bridging and mproving energy efficiency in buildings is installing insulation. Improving the insulation of a building is an example of a fabric-first approach to building design. In fabric first construction, the building elements are designed to reduce the reliance on external systems, such as mechanical or electrical heating or cooling systems. A fabric-first approach will maximise both airtightness and insulation.
The move to increase the insulation of buildings is not without its challenges, particularly in those areas which are difficult to insulate, e.g., existing buildings, solid wall buildings, window reveals, doorways and openings. Insulating in these difficult areas necessitates the use of very thermally efficient insulation.
The Spacetherm insulation range comprises highperformance aerogel insulation that can be bonded to various boards to suit specific applications. On its own, Spacetherm Blanket is a versatile material that is both vapour permeable and hydrophobic, making it ideal for solid wall insulation. It can be bonded to a magnesium oxide board to produce Spacetherm Multi. This can be as thin as 16mm, including 10mm of insulation and a 6mm board, making it ideal for breaking the cold bridges typically found at window reveals. Also, available in greater depths, it allows walls to be insulated to a thinner depth than would otherwise be possible. For example, 45 – 50mm of insulation would bring a typical wall down to the 0.3 W/m²K required for building regulations and EnerPHit certification. In addition, Spacetherm (CBS) cold bridge strips can easily be applied to minimise cold bridges. The cold bridge strips consist of Spacetherm Aerogel insulation encapsulated in polyethelene. Spacetherm CBS is an ideal choice for timber or steel frame structures and can be cut to various widths to suit different applications.
Meeting Part L – Solutions for Renovation
Many of the UK’s existing dwellings that require retrofitting to improve energy efficiency have solid masonry walls. A practical solution to improve the insulation in these buildings is to apply it externally. This can significantly increase the thermal performance of the wall and, depending on the insulation used, provide the optimal strategy in terms of hygrothermal performance. This approach allows the masonry to be entirely within the insulation envelope so that it is not cut off from the heat of the building and will not gain moisture as a result. If the insulation and external cladding or render are vapour permeable, the entire construction is breathable. Therefore, any water vapour from the room can permeate through to the outside with minimal difficulty. It is also an excellent use of thermal massing, as the stone would act as a heat sink within the insulation envelope.
However, many of these existing buildings are historically listed or in conservation areas, so it may not be possible to change their external appearance. Sometimes, the only way to insulate an existing wall is to provide insulation internally. This solution has several potential challenges. First, it takes up floor space within the property, especially critical where floor space is at a premium. Many smaller rooms cannot accommodate the depth of insulation required to bring a solid stone or brick wall down to the necessary u-value requirements of 0.3 W/m²K. A standard 215mm brick wall would take over 100mm of mineral wool insulation to meet this target, which could be up to 140mm when thermal bridging is accommodated. This would typically be offset from the wall with a cavity and could mean that such a system would require over 200mm of space from each external wall.
Aside from the loss of floor space, any internal listed features, such as cornicing, may need to be moved to bring them forwards onto the insulation. Electrical sockets and fittings and any other services on the external wall also need to be relocated. This will likely incur additional time and cost and could require specialist contractors.
Applying internal insulation to a solid external wall must consider the risk to its hygrothermal performance. Uninsulated solid masonry walls have had decades or perhaps hundreds of years of having the masonry at the temperature of the heated space inside. Cutting them off from the internal conditions could be detrimental to the hygrothermal performance.As these walls are exposed externally, they are subject to driving precipitation, which can be moved deeper into the masonry by solar radiation. It may have been the case that the heat from inside the building was either pushing this water back out, or allowing it to evaporate into the room, from where it would be dispersed by natural ventilation, especially if the building was drafty, as many older properties are. If internal insulation is applied to the wall, the masonry would be colder and less able to lose moisture. This could create a risk of water ngress between the insulation and the masonry or within the masonry itself.
When retrofitting a building, it is essential to consider the balance of heat, air, and moisture movement as a cohesive and unified strategy. Overly insulating a building without considering the effects on ventilation or the risk of condensation can result in disaster. For solid masonry walls, the risk of mismanaged moisture is particularly potent.
Based on years of extensive research and industry expertise, the A Proctor Group has developed a range of solutions to improve the energy efficiency of the fabric of the building.
A unique solution for airtightness in retrofit construction is Procheck Adapt, a vapour variable vapour control layer certified as a Passive House component for airtightness. This variable permeability, intelligent vapour control layer adapts its vapour resistance to suit the environment, becoming impermeable in the winter and allowing water vapour to permeate through in warmer and less humid periods. So, the membrane adapts to changes in humidity levels and allows the structure to dry out in the summer and sunny days in spring and autumn while protecting it from moisture overload in the winter and cold, wet days.
The Spacetherm® insulation range comprises highperformance aerogel insulation that can be bonded to various boards to suit specific applications. On its own, Spacetherm Blanket is a versatile material that is both vapour permeable and hydrophobic, making it ideal for solid wall insulation. It can be bonded to a magnesium oxide board to produce Spacetherm Multi. This can be as thin as 16mm, including 10mm of insulation and a 6mm board, making it ideal for breaking the cold bridges typically found at window reveals. Also, available in greater depths it allows walls to be insulated to a thinner depth than would otherwise be possible. For example, 45 – 50mm of insulation would bring a typical wall down to the 0.3 W/m²K required for building regulations and EnerPHit certification. In addition, Spacetherm cold bridge strips can easily be applied to minimise cold bridges. Cold bridging should be minimised, especially in a fabric first retrofit.
Addressing the challenge of internal insulation, Spacetherm Wall Liner is a thin thermal laminate of about the thickness of a standard layer of plasterboard. It consists of 10mm of Spacetherm insulation and a 3mm Magnesium Oxide board adhered to the wall to provide significant thermal retention compared to the uninsulated wall. Typically, it would bring a solid stone wall (with a starting u-value of around 2.3 W/m²K) down to a u value of between 0.7 and 0.9, representing a noticeable drop in energy lost through the wall.
New U-Value Assessment Tool
The A. Proctor Group has introduced dedicated U-value and Condensation Risk Analysis software that will help architects, designers, developers and contractors to accurately carry out assessments to ensure compliance with the latest requirements of the Part L building regulations. The software is an essential tool for meeting the new standards and improving the energy performance of new and existing buildings.
Request a Sample
Book a CPD
Technical Advice
U-Value Calculation
Specification Check
CAD Detail Review